AUTOMATION SYSTEMS
Automation is the use of advanced electronic and mechanical technologies to control and automate large and multifunctional machines and industrial platforms. Automation efficiency is important in terms of cost and time savings in high-volume production line applications such as industrial devices and machines in production stages that require highly precise positioning and payload, or in assembly lines where speed and repeatability are required but manual work is not economical. This is due to the high labor costs in these processes. It is used to collect electrical and electronic data related to the product and work machines during the production phase and to perform the necessary operations by system equipment and devices in line with this information. In addition, automation equipment is used in the manufacture of automation machines that today's manufacturing industry needs.
As DCZ Electric, we retail, wholesale and export all kinds of industrial automation devices and equipment. Made in Turkey. You can contact us for more information about automation devices, parts and equipment.
PLC Devices
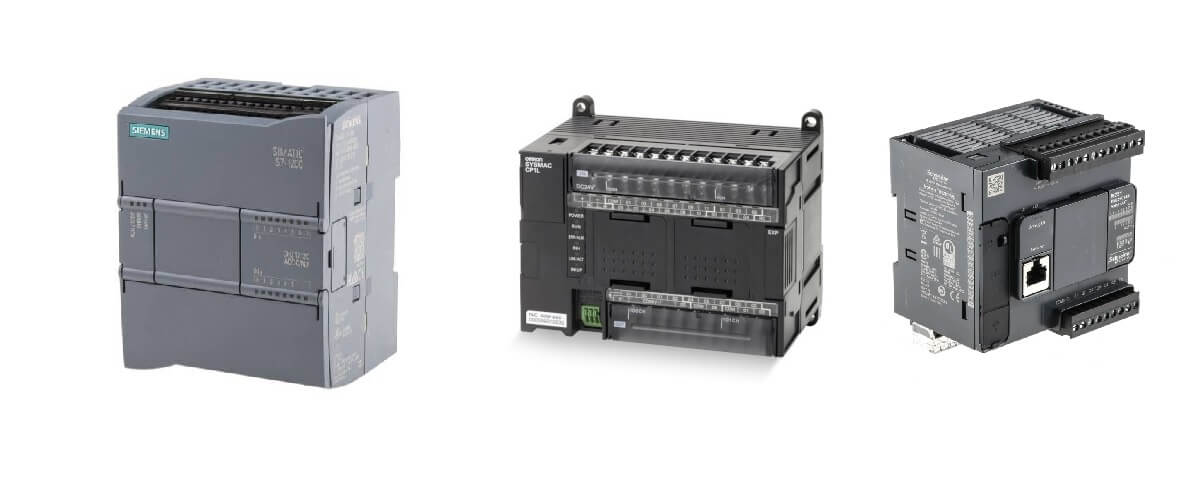
Automation is the use of electrical, mechanical and electronic devices to modify or improve manual processes. The term is often used to refer to machines, but can also apply to processes such as the use or control of computers to automate business processes. For example, when a machine is requested to make a production automatically, the machine is programmed according to the desired production amount and it is provided to manufacture by itself. The PLC controller receives instructions from a user and performs tasks accordingly. In this way, time, energy and efficiency savings are achieved in automation manufacturing and similar processes.
PLC stands for Programmable Logic Controller. It is an electronic device that can be programmed to perform certain functions. A PLC can be programmed to perform many different functions. It is essentially the use of electrical, mechanical and electronic devices to replace or improve manual processes in industrial automation.
AC Drives
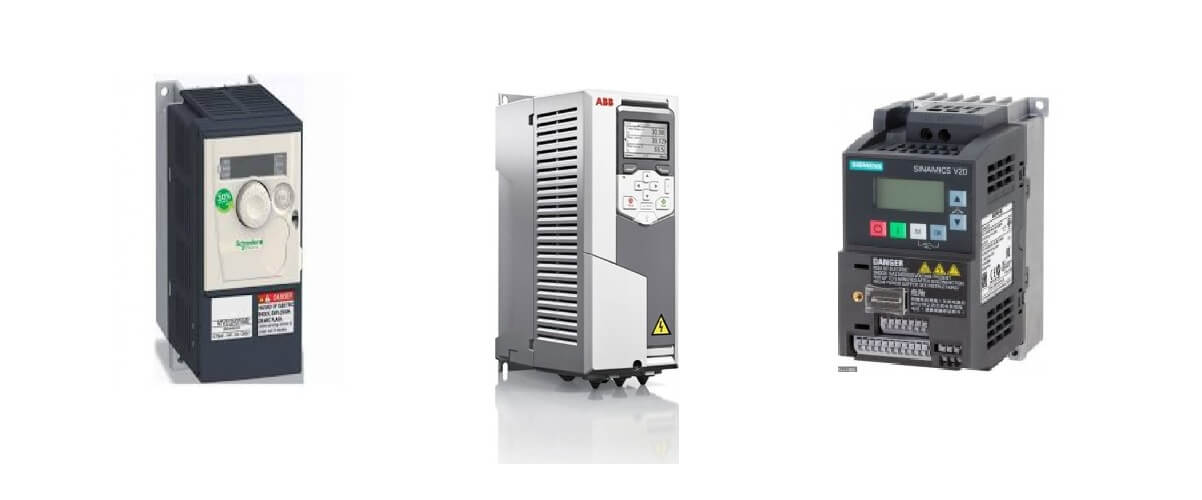
AC driver is a device used to control the speed and direction of the motor by using alternating current power instead of direct current. It is used to get more and balanced efficiency from the engines in the machines in the industrial manufacturing industry.
AC drive can be used to control the speed and direction of rotation of both synchronous and asynchronous motors. Synchronous motors are motors that have a constant speed of rotation while rotating in both directions. Asynchronous motors, on the other hand, do not rotate at a constant speed, their rotation speed changes depending on the working resistance. They are efficient for relieving heavy rolling resistance where high torque is often required.
The most commonly used AC drives are single-phase, three-phase and variable frequency drives. A single-phase drive consists of two sets of wires connected in parallel. A three-phase drive consists of three pairs of wires connected in series. A variable frequency drive operates using a combination of these two methods.
Servo Motors
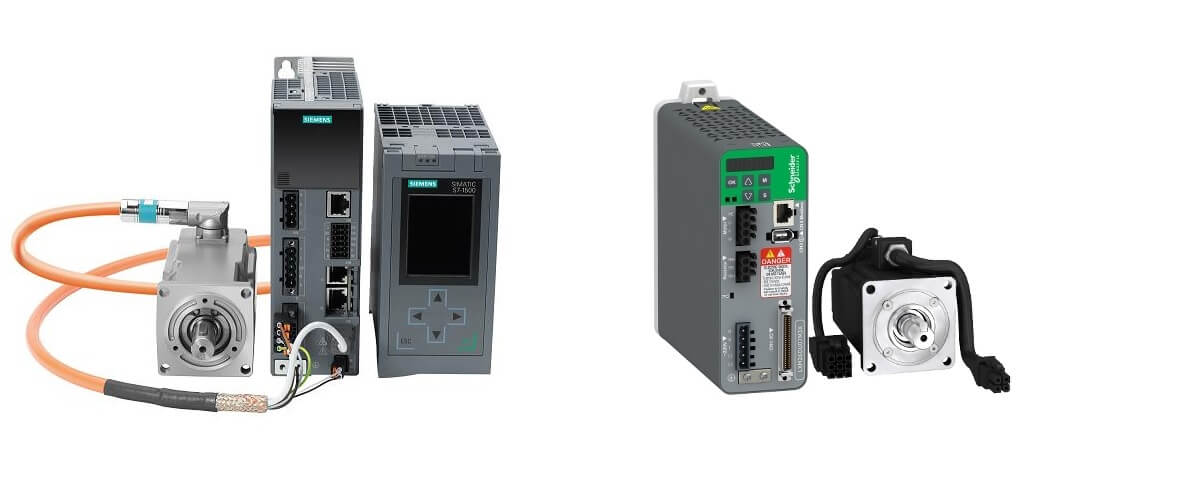
Servo motors drive a variety of industrial equipment, from simple robots to large mechanical machines, providing precise control over mechanical movements. The advantage of servos over analog controllers and electromechanical drivers is that they give a high-speed response within the specified limits and operate within the specified precision limits. Other than that, there are control advantages of using servos, including lower cost, smaller size, greater reliability, and fewer moving parts.
Servo motors are manufactured in many sizes and types. Commonly used servo motors include DC servo motors, AC servo motors, stepper motors, and voice coil motors. Servo motors can be operated with direct current (DC) and alternating current (AC).
It consists of a rotating shaft or armature held in place by a stationary stator. The armature is rotated by an external force such as a magnetic field, electric current, or a mechanical force. The motor is used to control the position of a load. The load can be an actuator, a valve, or another machine element.
Soft Starter
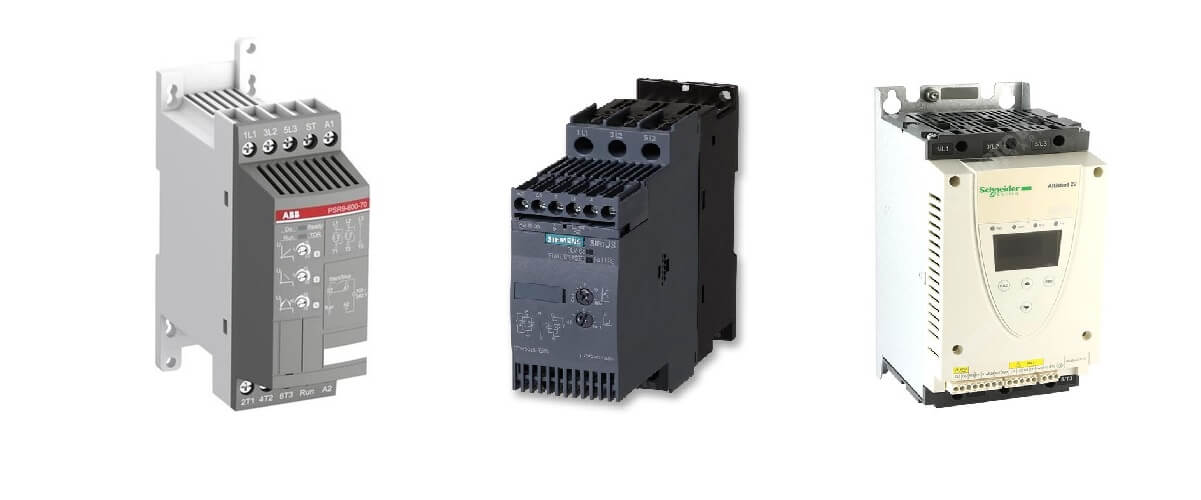
Asynchronous motor is a type of electric motor in which the rotor does not rotate synchronously with the magnetic field of the stator. In other words, the rotor rotates at a different speed than the stator. There are several advantages of using an asynchronous motor over a synchronous motor. One advantage is that they have no brushes to wear out. Another benefit is that they use less energy, making them ideal for battery powered devices.
Soft starter is an electronic device that enables a three-phase asynchronous motor to be started and stopped without damaging its winding. This type of motor has a rotor with three coils (or poles) and each coil is connected to a phase. The soft starter consists of a power supply, a microcontroller and a set of relays. When the relay contacts are closed, current flows through the stator winding, causing a magnetic field to be created and a voltage to be induced in the rotor. When this happens, the rotor starts to spin. The soft starter then opens the contact between the two phases while closing the third. By doing this, the torque produced by the motor is reduced, thereby slowing the rotational speed of the rotor.
Operator Panel
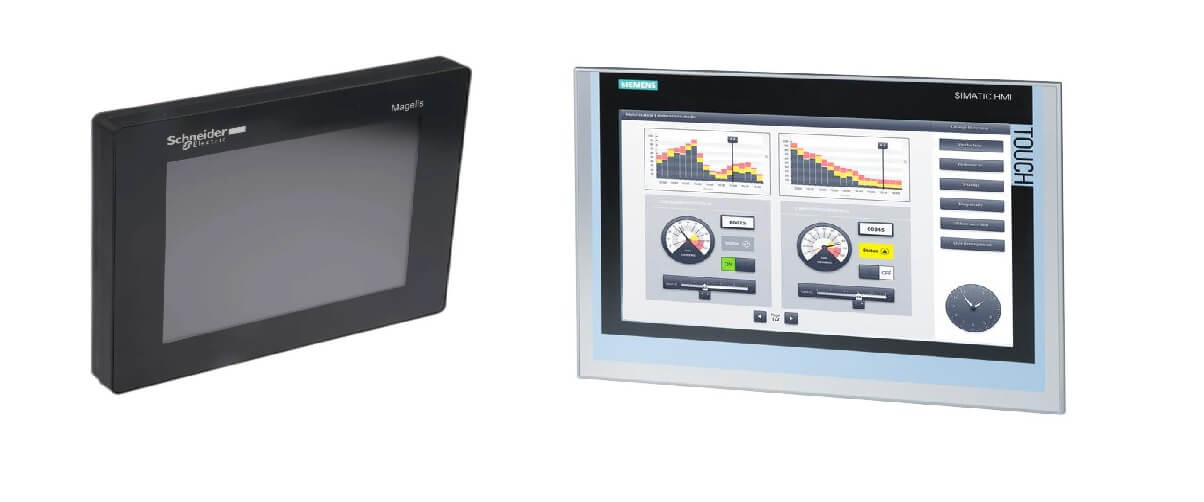
The operator panel is the unit that provides the interaction between the system and the user through the system panel. It can be a single panel or one of several. The operator panel provides the user with control, parameter setting, operating modes setting, control, completion setting, etc. It can be used for system control such as
The operator panel is where all the controls are. This includes switches, knobs, knobs, dials, and displays. There are many types of panels used in industry. Some are touchscreen based, while others may have physical buttons and buttons. All these panel equipment allow the user to control the automation system.
Power source
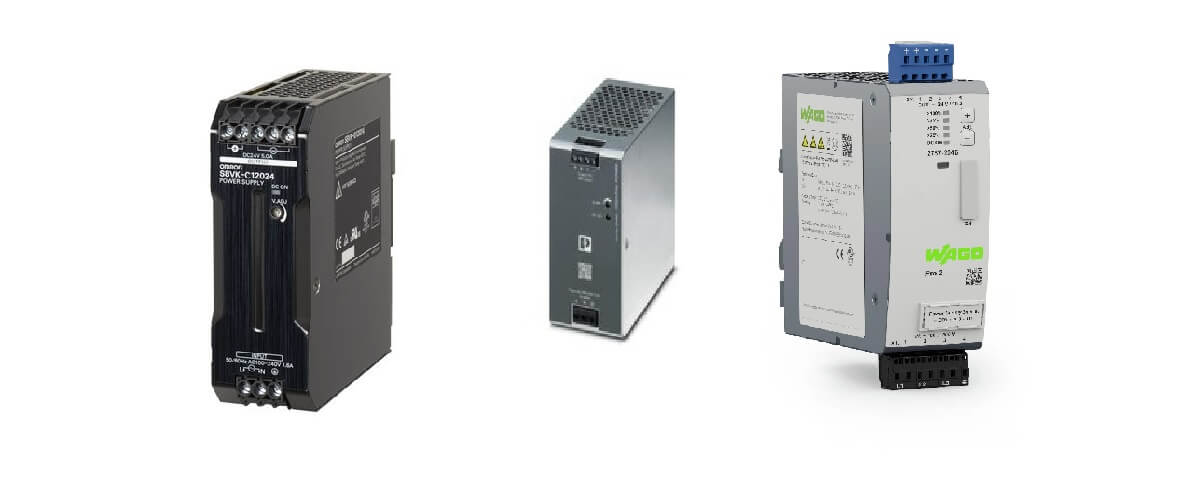
There are many types of power supplies used in the automation industry, but they can be divided into two main groups. One group is AC powered systems using alternating current (AC) mains electricity and the other is DC powered systems powered by direct current (DC). Each system has its pros and cons. AC powered systems have the advantage of being able to provide consistent voltage throughout the day regardless of whether the power is on or off. However, such a system requires a large amount of electrical wiring to distribute power from a central location to each device. This makes them difficult to install in any area that does not already have an available electrical outlet. DC powered systems do not require any external power supply, making them ideal for remote installations in areas where AC mains power is not available. They're also much smaller than their AC counterparts, making them easy to transport and store.
Servo Drive
A servo driver is a device that detects electrical signals and converts them into mechanical motion. Servo drives, which are microcontrollers, can be controlled by a microcontroller through the pulse width modulation data they sense. These signals cause the motor shaft to rotate at different speeds depending on the applied voltage. There are several types of servo drives available, but basically they all perform similar functions.
Commutator
A commutator is a device used to control the current flowing through a motor or generator. In other words, a commutator is a rotating metal plate in a motor or generator that allows alternating current to flow on its surface. This type of switching device changes its polarity, allowing current to flow in both directions. As electricity flows through it, the commutator causes an electromagnetic field moving around the electric coil inside the core of the motor or generator, and this magnetic field creates mechanical motion in the motor or generator shaft when the current changes direction and polarity. The time it takes for electricity to move from one pole to the other on the surface of the commutator is known as the commutation period or commutation time of the motor or generator; this is the time it takes for electricity to turn the rotor after the current changes' direction.